Cleaning machines Sales and Leasing
Eco-lander provides automated cleaning equipment that integrates pre- and post-cleaning processes, achieving seamless process integration and significantly improving production efficiency and yield. Its sealed design and high-efficiency filtration system meet cleanroom cleanliness standards, ensuring consistent high quality for every batch of products. Through digital control technology for monitoring and data recording, this equipment is suitable for critical components in the medical, electronics, and automotive industries. Additionally, it can effectively reduce solvent and energy costs, flexibly respond to large-scale production demands, and strengthen enterprises’ market competitiveness.
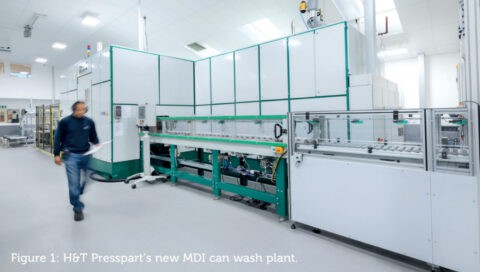
Hoeckh, based in Neuenbürg, Germany and founded in 1972, specializes in full vacuum close system cleaning machines that utilize sustainable, recyclable solvents. The advanced cleaning technologies include ultrasonics, spraying, immersion, high-pressure rinsing, vapor degreasing, chamber oscillation, rotation, and vacuum drying. No matter the complexity of your workpiece—whether it features deep blind holes or intricate geometries—Hoeckh systems guarantee efficient drying and high-purity cleaning results.
Hoeckh machine is renowned for its durability, with many systems operating for over 20 years while consistently delivering excellent performance.
6 Advantages of Hoeckh multiclean systems machine
- Efficiency:
High parts throughput and perfect quality - Reliable:
Integrated processing for stable operation - Universal:
Suitable for all common solvents - Eco-friendly:
Full vacuum for safety when handling solvents - Can be interconnected:
Prepared for industry 4.0 - Economical:
Low energy consumption and long solvent life
Mafac, located in Alpirsbach, Germany, has expertise with the vacuum water-based cleaning machines since 1974. Their systems utilize pure water or water-based detergents to effectively remove oils and fine particles from metals, plastics, and composite materials. The patented VAP (Vacuum Activated Purification) technology, combined with an energy-efficient vacuum drying technology, ensures high-purity cleaning for even the most challenging workpieces featuring deep, narrow blind holes, all in minimal time.
Mafac’s 4 Unique Technologies
Kinematic
Patented basic technology for cleaning and drying of uncomplicated workpieces. With simultaneous rotation of spray system and cleaning objects.
Vector Kinematic
The next dimension for complex geometries: Rotation and swiveling in combination. For increased versatility and improved results already in spray cleaning.
Vacuum Activated Purification VAP
Patented technology with pressure changes for highest demands and industry standards. For optimized cleanliness of hard-to-reach areas and tight structures.
Rotating Ultrasonic
Deep cleaning with rotation of basket, water jet and ultrasonics. For maximum film and particle removal on complex, finely structured components.
Hoeckh’s Mulitclean Duo System with Aqueous and Solvent-based:
The complexity of modern manufacturing processes and the further development of high-performance lubricants, as well as other processing aids, force many cleaning processes to the limit of their capabilities.
More and more frequently, the process chains in component manufacturing include multiple successive processing stages based on different lubricants, e.g. primary casting using oil followed by further processing with emulsions.
In these cases, pure solvent-based processes often leave residual salt spots or other inorganic impurities, while purely aqueous processes are often uneconomical with high oil content or expensive drying processes.
The solution is a combination of both processes in one system: economical degreasing with solvents, intermediate aqueous cleaning to remove any stains, and a final solvent rinse with energy-efficient vacuum drying.
Cleaning PCBA components after the reflow soldering process is crucial for enhancing the reliability of your electronic products. The fully automated, enclosed spray system—manufactured in Czech Republic, Europe—utilizes water-based cleaning agents to effectively clean PCBA of all sizes, shapes, and complexities.
Contaminants Removed
the advanced PCBA cleaning system effectively removes:
✔ RMA (Rosin Mildly Activated) flux
✔ No-clean flux
✔ Water-soluble flux
✔ Solder paste residues
✔ Dust and fingerprints
✔ Oxide layers before wire bonding
✔ Organic residues prior to conformal coating application